3.2. ESRS S4. Consumers and end-users
With our products and global positioning we contribute to the nutrition and well-being of millions of people, which requires responsible management of the entire supply chain. From the selection of raw materials, the cooperation with our suppliers on efficiency, social and environmental challenges, to the relationship with our customers, helping them to meet the changing needs of consumers and solve their sustainability challenges, while facilitating food safety.
Current and potential impacts, risks and opportunities
Positive
- Incidence: To make it easier to feed an affordable protein to millions of households around the world.
- Opportunity: Product safety and quality as a competitive advantage to lead the casing market.
Negative
- Incidence: Food security crisis.
- Risk: Failure to meet quality standards or a food safety crisis can lead to lawsuits and reputational damage.
- Risk: Losing market position due to regulatory requirements in terms of food safety.
Policies and commitments
- Code of Conduct.
- Business Practices Policy.
- Food Regulation Policy.
- Food Crisis Protocol. Product Withdrawal.
- Quality and Food Safety Management System.
Sustainability objectives
- 70% of our production plants with the highest AA rating in the Global Food Safety Initiative (GFSI) food safety certification. By 2024, this objective is met with 92% of the plants with this score.
Governance
- Board of Directors. Appointments, Remuneration and Sustainability Committee, Audit Committee.
- Executive Sustainability Committee.
- CEO.
- R&D and Corporate Quality Department.
Soporte
- Corporate Department of Regulatory Affairs.
- Customer Service.
3.2.1 Strategy
Casings are an essential element in the production of sausages and therefore in the food chain, allowing access to protein for millions of consumers. However, the vast majority are not perceived by the end consumer, especially in the case of cellulosic and fibrous products that are peeled by meat processors before sale. An increasingly conscious consumer when making purchasing decisions, which requires more transparency about the environmental and social impact of products, functional performance, safety and traceability of production throughout the value chain.
This trend is supported by government authorities, non-governmental organisations, industry organisations and associations and consumers through regulation and certification.
In this context, Viscofan has a wide range of products in the casing market, with sales in more than 100 countries, resulting in a complex landscape of functional and regulatory requirements that require a holistic approach on the part of quality management.
This approach starts with the development of products and applications to meet the demands of our customers and consumers and to comply with regulatory requirements for quality and food safety. It continues in the production facilities themselves, built according to the requirements of food safety standards; through training programmes in food hygiene and product safety; control of raw materials, which must meet specifications previously agreed with approved suppliers; systems for detecting inadequate materials in the production process; protocols for action in the event of a food safety crisis; pest control; control of hazardous materials; personal hygiene and visitor policies.
Interests and views of stakeholders
ESRS 2 SBM-2
To define this approach Viscofan comprehensively addresses the expectations of customers and, by extension, consumers, authorities and associations by providing public commitments (e.g. policies, technical documents, the Code of Conduct and the Supplier Code of Conduct) in its efforts to continuously improve its offering and proactively comply with the latest and future requirements, and to provide appropriate transparency in its activities.
Specifically, for Viscofan, interaction with customers is a very valuable tool for incorporating the interests and opinions of consumers in the development of the value proposition of products, especially in the protection of risks that may affect health or safety. It is worth highlighting the satisfaction evaluation and the system for complaints and grievances.
Viscofan's sales team has a satisfaction evaluation system that allows it to directly collect customer feedback by measuring four main parameters (product quality, delivery service, economic competitiveness and technical assistance).
Viscofan also has an integrated, comprehensive complaints and claims system that facilitates dialogue and communication to record, identify, follow up and analyse any communication of dissatisfaction with the product or service provided by the Viscofan Group to its customers. It is a transversal continuous improvement system in which the departments involved must analyse the cause of the dissatisfaction and provide corrective actions to be established in the organisation to avoid its repetition. Any dissatisfaction is analysed, making it possible to control both the material that is returned as a result of the complaints and compensations paid to customers.
For more information on how Viscofan interacts with its customers and thus indirectly with consumers and end-users, please refer to the stakeholder-related section of ESRS 2 General Disclosures.
Material issues, risks and opportunities and their interaction with strategy and business model
ESRS 2 SBM-3, ESRS 2 IRO-1
As casings are an essential ingredient in the production of sausages, Viscofan works to meet quality and food safety requirements, with excellence being a priority as the integrity of the food that reaches the final consumer depends in part on our casings. However, we are not exempt from the possibility of a food safety incident (see description below of this material incident), which would pose a risk to Viscofan both at regulatory level due to non-compliance with product quality standards and reputational risk (see description of these risks below). In this case, our response is deeply rooted in our strategy and business model. We have developed rigorous protocols to manage and mitigate any risk, ensuring a quick and effective response to protect both our customers and end-users.
By complying with the requirements of ESRS 2 SBM-3 paragraph 48, we include all consumers and/or end-users who could be materially affected by a food safety incident, i.e. any consumer of a sausage manufactured with a casing supplied by Viscofan. This includes those who may be affected by our own operations and value chain, through our products and through our business relationships.
We have identified material risks and opportunities arising from impacts and dependencies on our consumers and or end-users through our materiality analysis.
Below are the main IROs, their classification by category and their description, as well as their interaction with Viscofan's business, strategy and financial planning in accordance with disclosure requirement SBM-3 of ESRS 2.
Viscofan's objective is to avoid or mitigate risks, actively deciding how to respond and, at the same time, we seek to take advantage of opportunities, incorporating them into our strategy.
It should be noted that, for the incidence and material risks of consumers and end users, Viscofan has specific response plans to anticipate or mitigate possible future financial impacts. Viscofan works to prevent the occurrence and guarantee at all times the excellence of its products and services for both customers and the end consumer. For this purpose, Viscofan has a food safety system described in detail in point 3.2.2. of this ESRS.
Negative impact of food security crises
Viscofan's products, the casings, are part of the food chain and can therefore trigger an individualised food safety crisis incident, understood as the detection of a biological, chemical or physical hazard in food, feed or humans, which could result in, or indicate, a potential risk to public health, as defined in Decision (EU) 2019/300. Such an incident can be caused by a number of situations that can occur simultaneously:
- Conditions that put the population's health at risk.
- Failure to comply with any legal requirement.
- Threats within the Organisation (such as malicious contamination or sabotage, fires, etc.),
- Environmental threats (such as pandemics; disruption of essential services, such as water and energy supplies; floods and other natural disasters; failures/attacks in digital cybersecurity, etc.).
Within the categories established by ESRS S4 paragraph 10. a) this identified occurrence may affect consumers of products that may be intrinsically harmful to humans.
Viscofan has classified this incident into three types: emergency, major incident, and minor incident, depending on the effects on consumer food safety and also on Viscofan's brand image, each triggered by a management system.
In the 2024 financial year, there were no incidents or risks classified as emergencies or of a serious nature for which Viscofan had to activate the food safety crisis management procedure, or which gave rise to lawsuits or damage to Viscofan Group's reputation.
Risk of non-compliance with quality standards or a food safety crisis that could lead to lawsuits and reputational damage.
Non-compliance with quality standards in the production and distribution of products with an impact on consumer health can lead to a deterioration of the company's reputation. News of this kind can spread quickly through social media and other media, leading to a loss of trust in the company and a decrease in sales.
Furthermore, in addition to health risks, non-compliance with quality standards may give rise to legal claims for negligence or damages, which may result in fines by the competent authorities and an obligation to compensate the affected parties.
In the 2024 financial year, there were no incidents or risks classified as emergencies or of a serious nature for which Viscofan had to activate the food safety crisis management procedure, or which gave rise to lawsuits or damage to Viscofan Group's reputation.
Risk of loss of competitive position in the market due to regulatory requirements in terms of food safety and opportunity for competitive advantage to lead the casing market
Regulatory requirements in terms of food safety are strict and change frequently to protect consumer health. Should Viscofan fail to keep up with these changes and adapt its production processes, it could face regulatory penalties ranging from fines to a ban on the sale of its products.
This risk of loss of competitive position also affects as a positive opportunity in relation to the Viscofan Group's competitive advantage in terms of consumer health and safety as a lever to lead the packaging market.
In 2024, the Viscofan Group did not receive any relevant fines or penalties related to the failure to adapt its production processes to current regulations and any possible updates to these.
Viscofan seeks to lead the industry not only in innovation and quality, but also in food safety. We have a wide range of certificates that endorse our commitment to the highest safety standards, setting ourselves ambitious targets to obtain higher level ratings in these certifications (see more detailed description of this aspect in sections 3.2.2 and 3.2.3. of this ESRS), ensuring that our production processes and products comply with the regulations and requirements of our customers at a global level.
Thus, in 2024, there were no incidents or risks classified as emergencies or of a serious nature for which Viscofan had to activate the food safety crisis management procedure, or which gave rise to lawsuits or damage to Viscofan Group's reputation. In addition, Viscofan continued to maintain its global leadership in casings in the financial year.
Positive impact by facilitating access to global food and different groups
One of our sustainability commitments is SDG 2: "Zero hunger". Belonging to the food market carries with it a great responsibility, associated with providing millions of people around the world with access to basic nutrition. On this basis, within its purpose, Viscofan seeks to reach as many people as possible. Therefore, the development of products and solutions adapted to the needs of groups is an opportunity for Viscofan.
- Halal: In order to sell our products for the production of sausages destined for this community, it is necessary to have a certification issued by the Muslim authority of the exporting country, which certifies that a specific food or pharmaceutical product meets the requirements of the Islamic Law for consumption by the Muslim population and Islamic communities. A demographic that represents approximately a quarter of the world's population.
- Kosher: Requirement for the consumption of food by the Jewish community.
- We also manufacture products of vegetable origin for vegans and vegetarians.
- Promotion with meat and food companies for the development of the sausage production industry in India.
For reasons of competitive sensitivity, Viscofan does not break down the current or expected financial effects of this positive impact. However, they are part of some growth axes within the financial objectives set in the Beyond25 Strategic Plan.
3.2.2 Incident, risk and opportunity management
Policies related to consumers and end-users
ESRS S4-1, ESRS 2 MDR-P
Viscofan has several policies and commitments in place to manage material product impacts on consumers and end users, as well as the related material risks and opportunities. In the case of Viscofan, the occurrence of the negative impact described above could affect the right to an adequate standard of living and, in particular, health and the quality of food.
It is based on Viscofan's Code of Conduct (see more detailed description in section G1 Business Conduct), based on internationally accepted conventions on the defence of human rights, in particular the United Nations Global Compact, the United Nations Norms on the Responsibility of Transnational Corporations in relation to Human Rights, the OECD Guidelines for Multinational Enterprises, the Tripartite Declaration of Principles concerning Multinational Enterprises and Social Policy.
Viscofan's Code of Conduct, based on the search for respect for people's human rights, establishes among its guidelines the quality, safety and protection of the environment with our products. In the particular case of quality, it typifies the following:
"Our products do not pose unacceptable risks to life or health as we comply with the technical regulations applicable to the approval and marketing of our products. Quality is an essential component of our brand."
On this basis, the following policy and protocol have been articulated.
Food Regulation Policy
Its purpose is to ensure compliance with and adequacy to food regulations that are applicable to the activities and products of the Viscofan Group, identifying the necessary channels for their control, analysis and monitoring. This is an internal policy available to all employees on the corporate intranet, with the Corporate Regulatory Affairs Department being responsible for transparent communication of the food regulations applicable to the Group.
Food regulations govern the manufacture, processing and marketing of products intended for food consumption. It also covers products intended to be in contact with foodstuffs, such as packaging, plastics or inedible casings.
It must be complied with by Viscofan Group employees in all Group companies and is applicable to all activities related to food products, depending on their geographical scope of application at any given time.
The Corporate Regulatory Affairs Department is responsible for promoting, coordinating and supervising actions aimed at compliance with food regulations throughout the Viscofan Group, coordinating with those responsible for regulatory affairs in each of the companies that make up the Viscofan Group, who are responsible for food regulations in the territory in which the company operates, in application of the principles and content of this policy.
In complying with the policy, the Corporate Regulatory Affairs Department and the local Regulatory Affairs officers, considering interested parties, may contact external experts to obtain their opinion or, where appropriate, to coordinate or confirm their opinion and interpretation of the regulations applicable in their areas of activity.
In addition, the policy sets out methods to ensure that any new developments in food regulations applicable to Viscofan's activities are captured. These methods include, among others, membership of associations related to food regulations that inform of regulatory updates. It is worth highlighting the participation in the following alliances:
- Comité International de la Peliculle Cellulosique (CIPCEL). Based in Brussels, CIPCEL comprises the leading producers of regenerated cellulose film products.
- Collagen Casing Trade Association (CCTA). An association of leading producers of collagen casings worldwide that provides a forum for its members to discuss the development of legislation and actively promote the use of collagen casings.
- AINIA. Food technological centre based in Spain that supports the R&D tasks of its partners, especially in the areas of quality, food safety, sustainability, environment, design and industrial production.
- ANICE. The Spanish National Association of the Meat Sector is the biggest meat association in Spain to provide advice, represent and defend the sector's interests.
Food Crisis Protocol. Product Withdrawal
Based on the food regulation policy, the Viscofan Group has a general protocol for action in the event of a food safety crisis; identifying the elements to be taken into account to respond efficiently to it; establishing guidelines for action in the event of a product withdrawal or recall being necessary; developing an adequate communication plan and establishing the necessary mechanisms to monitor and review the events and their causes after the incident has ended, thus avoiding a repetition of the same.
This protocol covers all activities from the time the food incident is identified until the crisis is closed.
This is an internal document available to all employees on the corporate intranet.
This protocol has been approved by the Chief Executive Officer and the Directors of the departments involved in the event of a food safety crisis and product withdrawal/recall (Commercial, Finance, Operations, R&D and Quality, Legal, Investor Relations, Communication and Sustainability).
It applies to all products manufactured and distributed by all Viscofan Group companies, whether they are in their facilities, in transit, in the facilities of their distributors or in those of customers and consumers.
Processes for engaging with consumers and end-users on issues
ESRS S4-2
Viscofan, with its main product, casings, facilitates the production of sausages and with the exception of collagen casings, the usual practice is to remove them from the final product before packaging and subsequent sale by our customers, the meat processors.
The Group has a quality system that seeks to comply with the applicable regulations in this area in order to guarantee product quality and avoid incidents as far as possible.
On this basis, Viscofan's collaboration in terms of product quality is closer with customers, with specific channels managed by the commercial department which, among other aspects, cover product quality. These are the complaints and claims system and the customer satisfaction evaluation system.
In the event of a possible food crisis incident (product withdrawal), Viscofan has a protocol in place that seeks to safeguard the health of consumers and end-users, for which the departments involved are responsible as set out in the protocol detailed earlier in this ESRS.
Operating procedures are established based on: i) initiation of the incident with its receipt and communication; ii) activation of the Technical Committee on Crisis and valuation (initial data, risks, classification, decision on whether to withdraw the product, registration of the valuation); (iii) crisis management (activation of the Crisis Committee, performance of the functions set out in the protocol, product withdrawal/recall, finalisation and reporting); (iv) Communication guidelines.
Likewise, in order to manage this type of incident, Viscofan facilitates direct collaboration with customers, distributors, authorities or other stakeholders based on the established communication channels described in the following section.
As established in the Food Crisis Protocol, Viscofan conducts a simulation at least once a year to evaluate the effectiveness of its food safety crisis management procedures. This simulation assesses various aspects, including the product withdrawal and recall process. Additionally, it examines the channels of communication and collaboration with consumers. The simulation involves customers, distributors, and other relevant contacts, such as certifiers, external laboratories, and public health authorities. Furthermore, depending on the nature of the simulated incident, the exercise may also involve different subsidiaries within the Viscofan Group. The department responsible for the simulation is Corporate Quality Management, in collaboration with local Quality Management.
Processes to remediate negative impacts and channels for consumers and end-users to raise concerns
ESRS S4-3
The Food Crisis Protocol, once an incident has started, and depending on its possible effects on the consumer, establishes channels to ensure that sufficient human, technical and financial resources are available to manage the crisis.
First, if applicable, a decision is made on the activation of the product withdrawal/recall process based on the crisis category and the location of the product. A measure aimed at achieving the return, both by customers and end-consumers, of unsuitable products.
Once the affected product has been identified, affected customers and distributors need to be notified of the withdrawal or recall and their involvement. In addition, they should be given specific instructions on what to do with the product concerned (withdraw it from sale, notify customers, return it to the supplier, destroy it, etc.). A framework document is to be drawn up in case it is necessary to report the incident to the competent health authority (in accordance with the legislation applicable in each country).
Likewise, a series of measures necessary for the optimal resolution of the incident are established, with periodic monitoring of these measures to assess their effectiveness, through the preparation of situation reports until the incident is over.
Furthermore, Viscofan does not have a specific procedure for remediation when it is determined that a product has caused a negative impact on consumers as these are isolated events that must be analysed individually in conjunction with customers, consumers and relevant authorities, which may vary depending on the different countries in which Viscofan sells its products.
Communication channels
Food safety crisis and product withdrawal/recall protocol
In the specific case of a food safety crisis involving a product withdrawal, Viscofan has an action protocol in place that establishes the following communication channels, ensuring that all the agents in the value chain involved and affected are informed in a timely manner and can express their concerns:
- The crisis committee designates the role of a Spokesperson for crisis communication management. The Spokesperson is responsible for the constant contact with stakeholders and is therefore the receiver of requests and the sender of responses.
- The commercial department is in charge of contacting the affected customers to keep them informed based on the decisions made by the crisis committee.
- The Quality Management managers are the point of contact with the health authorities and the certification body Global Food Safety Initiative.
In the case of product withdrawal/recall seeking remediation or minimisation of the impact, once the affected product has been detected, it is necessary to notify the affected customers about the recall/recovery and its involvement. In addition, they must be provided with specific instructions on what they must do with the affected product (remove it from sale, notify customers, return to supplier, destroy it, etc.).
Ethical Channel. Integrity Line
Viscofan has an Ethical Channel. Integrity Line that seeks to facilitate accessibility, knowledge and promotion so that employees, customers, suppliers or other interested stakeholders can express their concerns. See more details about it in ESRS G1 – Business Conduct.
Effectiveness of communication channels
The crisis simulation exercise carried out by Viscofan aims to guarantee the effectiveness of this procedure and involves customers, distributors and other affected contacts, testing the correct functioning of the communication channels.
The Ethical Channel. Integrity Line is unique for all Group companies and for all violations or irregularities. It is accessible through the corporate website and the Viscofan intranet and has the following characteristics:
- It will allow the communication of information 24 hours a day 7 days a week by completing a written form. This form is available in several languages.
- At the request of the informant, the information may also be presented through a face-to-face meeting that must take place within a maximum period of seven days. Where appropriate, the whistleblower shall be warned that the communication will be recorded and informed of the processing of his or her personal data. The face-to-face meeting may be replaced by a video conference meeting or other secure telematic means that guarantee the identity of the whistleblower, and the security and confidentiality of the communication.
- Anonymous submissions are permitted.
Communications are made on the basis of a procedure that provides the necessary guarantees for informants and other parties concerned, in particular as regards protection against reprisals when using this system.
Taking action
ESRS S4-4, ESRS 2 MDR-A
Actions related to food safety incidents, opportunities and risks
However, in order to prevent, mitigate and repair an event of relative importance and the risks associated with it, Viscofan promotes a food safety and product quality system in its operations, seeking to ensure the safety of consumers with the packaging and ingredients used, and promoting an effective incident management system. Following on from this, Viscofan seeks excellence in food safety as a competitive advantage. The measures and resources allocated are as follows:
Food safety and product quality system
Viscofan has a quality management system, managed and coordinated by the Corporate Quality Management department, which is based on the following guidelines to ensure that the measures implemented are necessary and appropriate to avoid, as far as possible, the occurrence of a negative impact:
- Hazard analysis and critical control point. Viscofan has a hazard analysis and critical control point (HACCP) system in place. Hence, an inter-disciplinary team assesses every step of the production process to detect possible hazards (physical, chemical and microbiological pollution, including allergens), identify critical control points, establish relevant controls and take any required corrective action. The system is annually updated in line with any changes in the production process.
- Compliance with applicable legislation. The production of casings is increasingly regulated in the area of food safety by countries and supranational institutions, creating a growing and constantly changing battery of rules. This regulatory framework directly affects the activity of different production plants due to laws in the country of origin and requirements in the receiving countries, and internationally recognised standards. Viscofan has a specific Patents and Regulatory Affairs department to update and monitor regulations.
- Product traceability and certification. Viscofan operates a product traceability system that enables us to identify, at any time and in full detail, the history of every unit and even sub-unit sold, from receipt of raw materials to product use by our customers. In Europe, Viscofan has fully implemented the food traceability system in accordance with Regulation (EC) 178/2002.
- Audit and certification. To ensure that our product safety and food hygiene systems comply with requirements, our production processes are audited internally on a regular basis. Our production facilities are also continuously audited by the health authorities, numerous customers and certification authorities. In this regard, all the Group's plants are Global Food Safety Initiative (GFSI) certified, which is an initiative of key food industry partners working together to drive continuous improvement in food safety management systems around the world.
Viscofan also has internationally recognised certifications for meat processors to approve their suppliers and market their products in the world's main distribution chains, and as part of its commitment to food safety and hygiene, it seeks to improve on the marks obtained with these certificates. The certificates demonstrating the Group's commitment to workplace safety, health and product quality are shown below:
Country | Plant | Certifications | |
---|---|---|---|
Food safety | Quality | ||
Spain | Cáseda | BRCGS Packaging Materials | ISO 9001 |
BRCGS Food Safety | |||
Urdiain | BRCGS Packaging Materials | ||
Czech Republic | Ceske Budejovice | BRCGS Packaging Materials | ISO 9001 |
BRCGS Food Safety | |||
Germany | Weinheim | BRCGS Food Safety | ISO 9001 ISO13485 |
Alfhausen | BRCGS Packaging Materials | ISO 9001 | |
Serbia | Novi Sad | BRCGS Packaging Materials | ISO 9001 |
BRCGS Food Safety | |||
Belgium | Hasselt | BRCGS Packaging Materials | ISO 9001 |
China | Suzhou | BRCGS Packaging Materials | ISO 9001 |
BRCGS Food Safety | |||
Canada | Montreal | BRCGS Packaging Materials | |
US | Danville | BRCGS Packaging Materials | ISO 9001 |
Montgomery | BRCGS Packaging Materials | ISO 9001 | |
BRCGS Food Safety | |||
New Jersey | FSSC 22000 | ISO 9001 | |
Mexico | San Luis | BRCGS Packaging Materials | ISO 9001 |
BRCGS Food Safety | |||
Zacapu | BRCGS Packaging Materials | ISO 9001 | |
Uruguay | Pando | BRCGS Food Safety | ISO 9001 |
Brazil | Itu | BRCGS Packaging Materials | ISO 9001 |
BRCGS Food Safety | |||
Ermelino | BRCGS Packaging Materials | ||
Australia | Sidney | FSSC 22000 | ISO 9001 |
Product safety vis-à-vis consumers and end-users
The Quality Management and Regulatory Affairs departments, supported by Customer Service, are globally responsible for the food safety of the packaging and compliance with applicable laws, regulations and standards.
In this regard, in addition to third-party certifications, risk analyses are carried out for certain ingredients, as well as the monitoring, analysis and assessment of specific regulations and standards that may have an impact on the business.
Product recall incident simulations
Every year Viscofan carries out simulations of a product recall incident, which are recorded in an internal information storage tool. The crisis drill, including product withdrawal/recall, will involve customers, distributors, other affected contacts (certifier, external laboratories, public health, etc.), as well as the different subsidiaries of the group as appropriate.
In 2024, Viscofan carried out a crisis simulation exercise with satisfactory results.
Actions related to relatively major food facilitation incidents
Communities: With a view to the production and marketing of Halal and kosher certified casings to facilitate the feeding of an affordable protein to these communities, Viscofan has such certifications in several plants.
Vegetarian, vegan and flexitarian population: Viscofan with its vegetable-based casings, both non-edible such as cellulose and fibrous, and edible such as the Veggie casing, contributes to the development of a wider variety of products. In particular, in 2024 it worked with several companies producing plant-based sausages to develop recipes to improve the taste and quality of the ingredients.
Development of the sausage production industry in India: With a sales office located in Bangalore staffed by sales and technical support people, and a product application plant, Viscofan has worked in 2024 with meat processors in the development and promotion of different recipes for both meat-based and plant-based sausages.
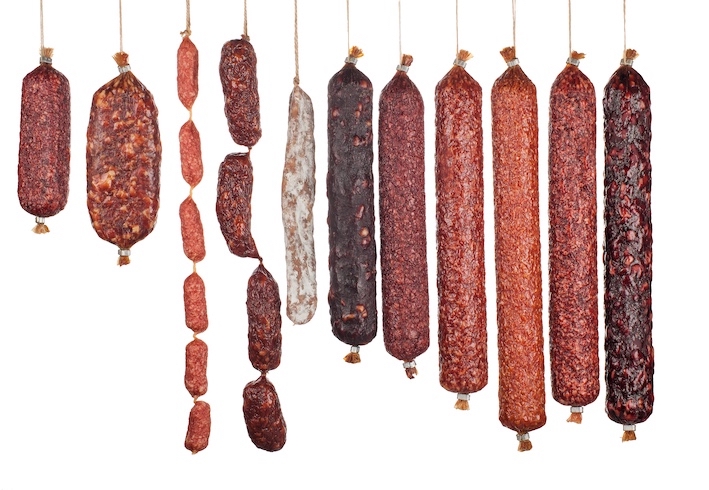
3.2.3 Parámetros y metas
Targets related to managing material adverse events, driving positive events and managing material risks and opportunities
ESRS S4-5, ESRS 2 MDR-T
Viscofan does not have a specific target related to this aspect framed within the Sustainability Action Plan due to the fact that no specific indicator has been identified that can measure the objective of avoiding food safety incidents that could affect consumers and end users of the products and, by extension, reputation. However, it seeks to meet this objective by improving the management of food safety at the sites, and by seeking customer satisfaction. To this end, the elements that help to measure Viscofan's performance are as follows:
- Qualification of food safety certificates: Viscofan is seeking to improve its score under the GFSI certificate in this area, so that in 2024 92% of the plants have obtained the maximum score (AA) in the certificate, a considerable improvement compared to 45% five years ago and above the target of 70%.
- Customer satisfaction: the latest global customer satisfaction survey carried out in 2024 showed an overall customer satisfaction rating of 85, providing information that serves as a basis for catalysing improvements in customer service, and in particular product quality.
- Integrated Grievance and Grievance System: In 2024, a total of 3,612 complaints were registered in our systems, including both service and administrative or product complaints.
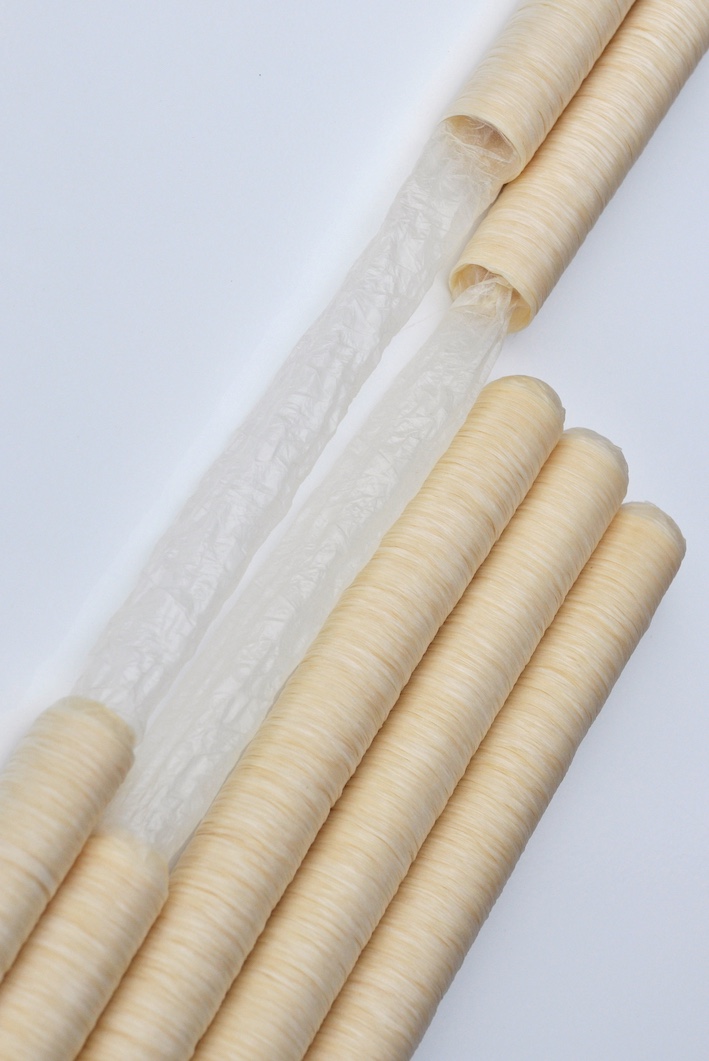